How 3d printing is shaping manufacturing
- students4enterpris
- Apr 7, 2022
- 3 min read
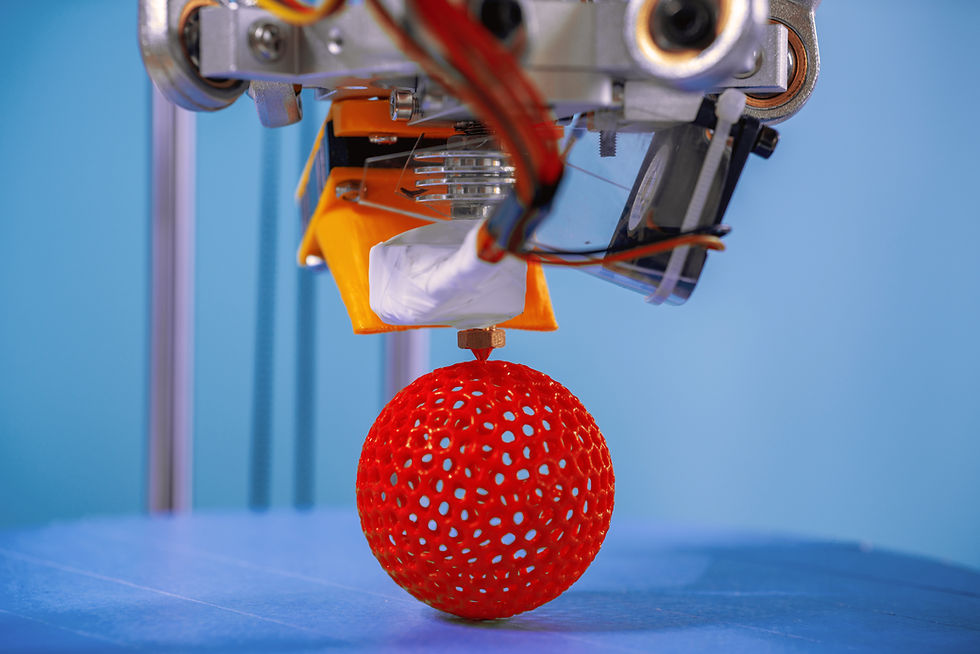
Popularly known as 3D printing, additive manufacturing technology has transformed traditional manufacturing. By simplifying the modes of production and allowing for greater customisation it has brought in a new wave of innovation. The recognition of its benefits has led to wide adoption from companies such as L'Oreal to Airbus.
The technology produces an object by printing subsequent layers one at a time, hence the name ‘additive manufacturing’. It also relies on Computer Aided Design (CAD) software. It is considered to be a general-purpose technology as it has the potential to be used across several industries from auto parts to jewellery.
The worldwide market for 3D printing products and services was valued at around 12.6 billion U.S. dollars in 2020. The industry is expected to grow at a compound annual growth rate of 17 percent between 2020 and 2023. North America accounts for the maximum share in the global market, followed by Europe. Asia Pacific is expected to grow at the highest CAGR in the next years.
3D printing has certain advantages over traditional manufacturing which will be delineated below. Firstly, 3D printing has the potential to produce complex and intricate designs which were previously very difficult to produce using traditional manufacturing techniques. For example, architectures such as honeycombing within steel panels or geometries posed challenges as these structures were too fine to mill.
Secondly, 3D printing manufactures products in a single go. A big part of the additive advantage is that pieces that used to be moulded separately and then assembled can now be produced as a single piece. A Harvard Business Review article evidences the benefits of printing a pair of sunglasses: “The 3-D process allows the porosity and mixture of plastics to vary in different areas of the frame. The earpieces come out soft and flexible, while the rims holding the lenses are hard. No assembly required.”
Thirdly, 3D printing is more flexible compared to the traditional manufacturing techniques. Traditional manufacturing techniques are most suitable for economies of scale. However, this is also one of the reasons for the lack of flexibility in terms of design. In 3D printing, each unit is produced separately and independently. Hence, it is very easy to modify each design for production. The designs can adapted to the latest trends or to improve a product. Also, the initial setup stages are far fewer than traditional manufacturing techniques.
Finally, 3D printing reduces raw material wastage in the manufacturing process. Hence, it lowers the carbon footprint and supports the circular economy. 3D printing can therefore be of great benefit to companies with sustainable development goals who are conscious about reducing their environmental footprint across the supply chain.
One notable disadvantage of 3D printing is the cost of the technology. The price of 3D machinery depends on the purpose and expected quality; however, it is generally expensive which poses a problem for start-ups or SMEs. For big companies the investment in 3D printing technology can be justified by the long-term benefits and increased innovation capability that they will receive through rapid prototyping.
There are several examples in industry of the widespread adoption of 3D printing among large companies. French cosmetics manufacturer L’Oreal has been using 3D technology for more than 20 years. It is now using 3D printing for producing human skin through bioprinting. The 3D printed skin could be used to test products and reduce the controversial use of live animals. Similarly, in aerospace, Airbus was able to create bio-inspired panels that weighed 15 percent lighter than panels made using conventional production methods. They also produced complex internal support structures, such as lattices inside the panels, without incurring additional manufacturing costs.
3D printing is an important component of industry 4.0. It has already revolutionised the capabilities of the manufacturing industry; however, it is yet to reach its full potential. In the coming years, we can expect to have new materials and improvised machinery which will make the process cheaper, faster and more reliable.
In the startup world disruptors are paving the way for a new era of 3D printing. Stämm Biotech raised $17 million for its next generation, 3D printed bioreactor. ICON raised $185 million in a Tiger-led round to build more homes with its 3D printing technology and is now approaching $2 million valuation. Big companies as well as start-ups are coming up with innovative ideas which are getting attention from investors. Innovation will be a key factor in shaping the success of the 3D printing industry and its subsequent impact on manufacturing.
References:
https://hbr.org/2015/05/the-3-d-printing-revolution
https://www.cnbc.com/2019/11/09/3-d-printing-disrupts-12-trillion-manufacturing-industry-globally.html
https://www.manufacturingtomorrow.com/article/2018/03/how-3d-printing-is-impacting-manufacturing/11190
https://techcrunch.com/tag/3d-printing/
https://www.manufacturing.net/industry40/article/13224762/how-3d-printing-will-impact-the-manufacturing-industry
https://manufacturingdigital.com/technology/what-impact-will-3d-printing-have-manufacturing-and-logistics
https://www.airbus.com/en/newsroom/news/2018-04-bridging-the-gap-with-3d-printing
https://www.statista.com/statistics/315386/global-market-for-3d-printers/
Comments